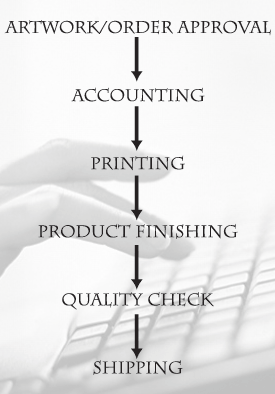
Our Process
The initial stages of an order involve client / representative contact. Our customer service representatives will go out of their way to construct and finalize your order in a fast and friendly way.
The next stage the order will go through is our accounting stage. Here the order will be checked for accurate information for shipping, sizes, quantity, payment information, etc... We cannot produce any products without payment for them first. Any special needs/requests are on a per order bases. If you have a special request, please notify one of our friendly representatives. Once the order information checks out and we have verification of payment information/details, your order moves on.
The following stage is where the products for the order are produced in our state of the art production facility. Our skilled production team will work hard to get the order on its way efficiently and on time.
Each order goes through the product finishing stage. This is where each order gets its final touches. Exact sizes can not be guaranteed as prints can fluctuate up to ½" per linear foot. Example: Finished size of a 12' (144") print can be up to 6" short. We will produce as closely as possible to the indicated size.
We strive to provide quality products that you can call your own. This is why we run every product through our very own quality test. We want to make sure our products are shipped in the condition you would expect to receive the products.
Outside of the customer-employee interaction, there is a great deal of technology in use—we can offer such great turnaround on our products because we have industry-leading technology at work 24 hours a day, that coupled with skilled shop staff equals out to an exceptional product.
Color Management — Because color is important!
Every morning our printers are calibrated. We also use HP-Colorwin to help make sure colors are what they’re supposed to be. A great deal of attention is paid to how colors are coming out, we know that color is a crucial aspect of a design.
Artwork Specifications
General File Information & preferable file types
When submitting artwork, files must be ready to print with no bleeds. We do print to the edge, but still recommend that you don’t have any important information (like small text) within an inch of the edge of your design. The document should not have objects extending outside the dimensions of the area that will be printed, this may cause problems when resizing and preparing the document for printing. Make sure all fonts have been created to outlines.
We print in 4-color CMYK and 6-color CMYKLCLM, please keep this in mind when submitting files for printing as color tone shifting may occur if file is submitted in RGB or other color spaces. If there is a specific PMS color required for your project please let us know so we can verify that you have the proper color mix in your file.
Please review your artwork at full size before submitting as we are not responsible for output quality (including color, clarity and final output) when printing customer supplied files. We do our best to ensure that your final product is what you want, but we aren’t able to do so without you putting in your part. Trust us when we tell you something won’t look good or turn out as you imagine it will.
The files we prefer are vector based .eps (Adobe Illustrator, version CS5 or lower). Make sure all text has been converted to outlines. A high resolution (600-800 dpi) jpeg, pdf, or tif may also work. Please flatten all layers when submitting documents from Photoshop.
Exact sizes can not be guaranteed as prints can fluctuate up to 1/2” per linear foot. Example: Finished size of a 12’ (144”) print can be up to 6” short.